Aldridge leverages an in-house Virtual Design & Construction (VDC) team to design prefabricated builds that allow for seamless field installation of infrastructure. Our in-house VDC team works collaboratively with the PreFab team and craft workforce to utilize a number of technologies to design, prefab, and install infrastructure solutions for even the most complicated project sites. This team supports model coordination, prefabrication installations, shop drawings, and augmented reality solutions. Work includes BIM/3D modeling, prefabrication strategies, design detailing, manufacturing, and project installation.
Return of the Turkey Fry
After a COVID hiatus, our favorite Thanksgiving tradition made a triumphant return today! Deep-fried turkey is the star of this Thanksgiving meal that has been an Aldridge tradition since 1991. Fleet Services welcomed guests to our Libertyville headquarters to share a meal, enjoy live music, a silent auction benefiting the Juvenile Diabetes Research Foundation (JDRF), and participate in a food drive.
Innovations Spotlight - Adjustable Roller Opener
When drilling large-diameter shafts in rock, drilling and hammering the complete diameter of the shaft in one shot requires extremely large tooling and support equipment. Moving all of this equipment and tooling from shaft to shaft is not ergonomic, time-consuming, and limits the crew's productivity.
National Fire Prevention Month
Lynn Meersman, Vice President of Estimating here at Aldridge, tells her story about how she almost lost her brother as a child, due to fire alarms not in close enough proximity to his crib. She discusses the importance of learning how to use a fire extinguisher, having an escape plan for your family, and changing out your fire alarm batteries annually as a safety precaution.
Top 600 Engineering News-Record Announcement
For over 40 years, Engineering News-Record (ENR) has published an ongoing list of the top 600 specialty contractors. The rankings are adjusted according to the previous year’s rankings, revenue, and the percentage of revenue by market. This draft unveils top-ranked firms' takeaways and plans for the future. After the two-year mark of Covid-19 disruptions, Aldridge Electric comes out on top!
A Safety Perspective from O’Brien Mills via Line Contractor Magazine
Suicide Prevention - Mental Health Resources
With a suicide rate that is four times greater than the national average, the construction industry is facing a crisis. In 2018, the CDC released an updated study of suicides by occupation. Construction had the most suicides and the second highest rate of suicides of all the industries. That rate is four times greater than the national average and five times greater than that of all other construction fatalities combined. This affects us all.
WHAT ARE THE WARNING SIGNS?
Warning signs may help you determine if someone is at risk for suicide. If you know someone who exhibits any of the signs below it is time to seek help:
TALKING ABOUT...
Wanting to die
Great guilt and shame
Feeling trapped or being in unbearable pain
Being a burden to others
Saying goodbye
FEELING...
Empty, hopeless, or having no reason to live
Extremely sad, more anxious, or agitated
Unbearable emotional and/or physical pain
Lonely
CONCERNING BEHAVIORS
Making a plan or researching ways to die
Taking dangerous risks or acting reckless
Increasing the use of alcohol or drugs
Acting anxious or agitated
Sleeping too little or too much
Withdrawing from friends and family
Displaying extreme mood swings
Giving away important items
WHAT ARE THE RISK FACTORS?
Risk factors do not cause or predict a suicide. Rather, they are characteristics that make it more likely that an individual will consider, attempt or die by suicide. It is important to be aware of these risk factors when supporting others:
Mental health disorders, such as depression and anxiety
Alcohol and other substance use disorders
Previous suicide attempt or family history of suicide
History of trauma
Major physical or chronic illnesses
Recent job or financial loss
Recent loss of relationship
Easy access to lethal means
WHAT CAN YOU DO?
By promoting resilience and connection with others during a mental health emergency, you can help lessen the likelihood of suicidal behaviors. If you or a loved one are considering suicide, establish protective factors by taking the actions below:
GETTING HELP
Suicide is preventable! Seeking help is the first step. We share this information to promote our IIF Culture. We need everyone to care for one another. It’s not enough to focus on getting people home safely at the end of a shift. For at-risk employees it’s sometimes more important to get employees back to work safely from home. Using the resources shown can help save a life.
There’s Never Been a Better Time to Become a Part of the A-Team!
Farewell Summer 2022 Interns!
Celebrating another great summer with our biggest team of interns yet - 50! During the three months they spent at Aldridge, the Class of 2022 made meaningful connections with industry professionals, learned more about their areas of interest, and were shown what a career path in construction could look like for them.
Inaugural Women Of Aldridge Event
The Inaugural Women of Aldridge event took place on August 9th and brought women of all walks of life together for a day of empowerment. The mission of this group is to actively promote Women in Construction through professional development, networking, and mentorship, and to provide an open forum for encouragement and support. We are proud to support the Women in Construction movement and honored to have these hard-working women helping build America’s infrastructure.
Over 100 Aldridge women descended upon our new Chicago O’Hare office for a day of interactive events, breakout sessions, and personal stories. With work coast-to-coast, it’s often hard to get everyone in one place at one time and this was an outstanding opportunity to bring together those from Maine, California, and everywhere in between!
Here are some highlights:
A curated group of Aldridge women was chosen for a panel discussion surrounding issues women in construction face within the industry.
Small group breakout sessions allowed titles to be left at the door, as we asked hard-hitting questions on what’s next for the overall growth of Aldridge.
Guest speaker, Susan Silver, shared her career advice from years of working for Fortune 500 companies and now being a small business owner, as well as the adversity she experienced during her career progression.
Thank you to everyone who came to this first-of-its-kind event with an open mind and willingness to share. As we work toward a more inclusive workplace culture, and strive to develop a community of diverse individuals able to express their true selves, we look forward to many more events like these.
We are proud to be the Women Of Aldridge.






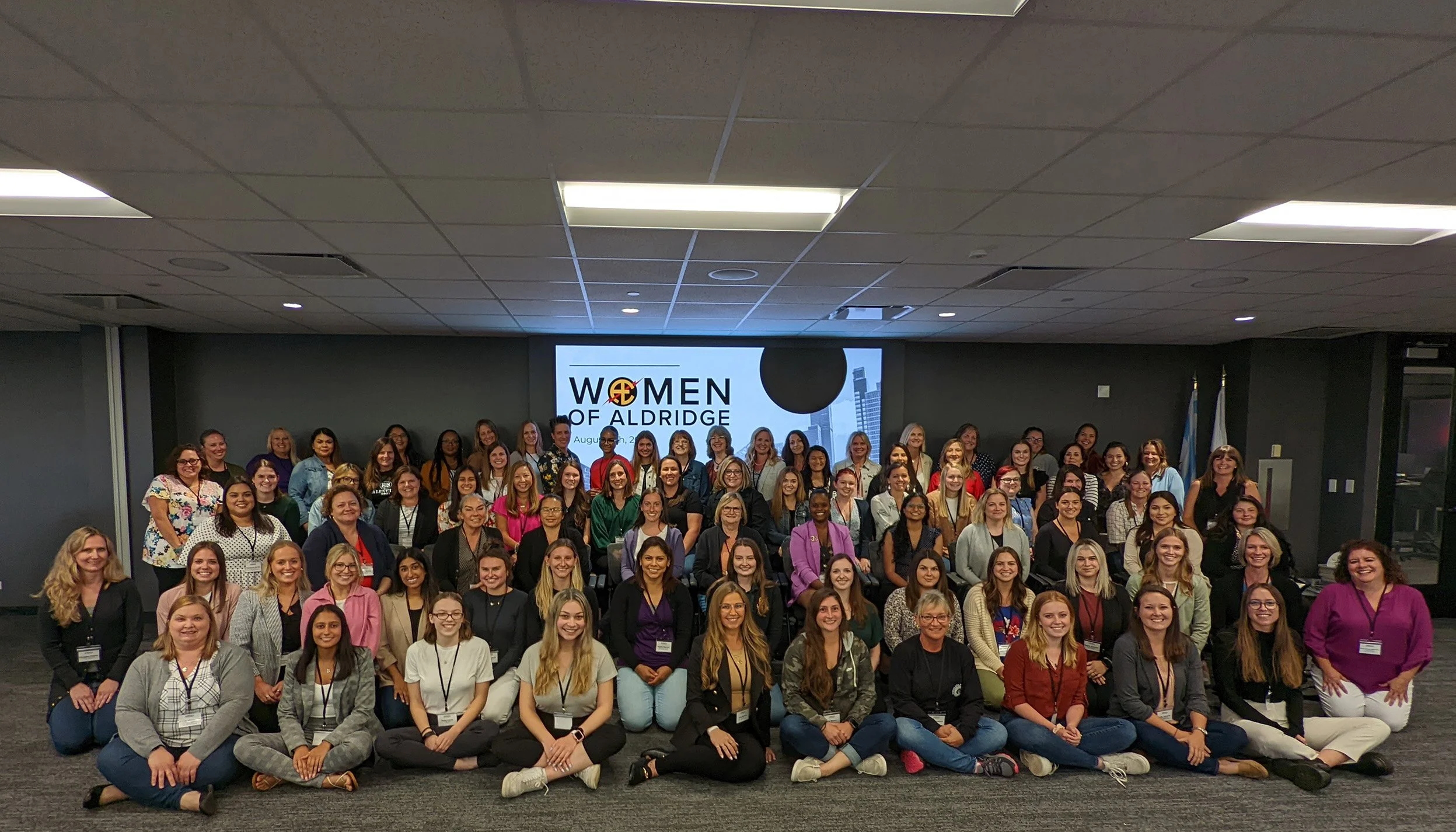
ADSC Honors Aldridge With Safety Award
With nearly one million work hours dedicated to providing foundation drilling solutions to the infrastructure industry, Aldridge strives to remain Incident and Injury Free at every hour. That’s why we were honored to receive the ADSC safety award celebrating that commitment.
The annual award was presented to Senior Vice President, Zach Kane, at the Association of Drilled Shaft Contractors (ADSC) Annual Meeting in Stowe, Vermont. As a long-time member of the ADSC, Aldridge is always looking for innovative ways to improve job site safety on complex drilling sites across the country. Our commitment to safety never wavers.
Aldridge Receives Virginia Contractors Safety Award
Since establishing our footprint in the Mid-Atlantic, Aldridge has worked on numerous high-profile power and transportation projects throughout Virginia. At the 2022 Virginia Transportation Construction Alliance (VTCA) annual meeting, Aldridge was recognized with a safety award for providing a safe working environment to our employees and the traveling public.
At Aldridge, safety is paramount. As we continue to take on new challenging infrastructure work in Virginia, we are committed to providing our passionate people with the knowledge and tools they need to make safe decisions and carry a safety mentality with them - at home or at work.
Heat Stress Awareness
As we enter the hottest months of the year, it is vital to remain hypervigilant in monitoring for heat stress. Heat stress can increase the risk of injuries and is a serious condition that occurs when the body can no longer control its internal temperature causing a multitude of dangerous effects. People can experience heat rash, cramps, exhaustion, and stroke. Aldridge employees are trained annually through a comprehensive Heat Stress Prevention Program which provides extensive awareness through best practice education.
Causes of Heat Stress:
Dehydration
Lack of airflow
Sun exposure
Hot and crowded situations
Heat Index
Aldridge employees are provided a heat guide that shows what the temperature feels like to the human body when relative humidity is combined with the air temperature. When the body gets too hot, it begins to perspire or sweat to cool itself off. An excessive amount of sweating in extremely hot temperatures can lead to heat stress, hyperthermia, heat stroke, and many more negative effects. It is extremely important to be aware of your surroundings and prepare for the temperature you will be working in. This will allow for a safe schedule encouraging everyone to take proper care of themselves and each other. Also, ensuring equipment is safe to use and any modification needed to be implemented for the day's work based on extreme weather conditions.
Low-risk conditions are to be handled with caution. This occurs when the heat index is between 80 and 90 degrees Fahrenheit.
Moderate risk conditions are to be handled with extreme caution. This occurs when the heat index is between 91 and 103 degrees Fahrenheit.
High-risk conditions = DANGER. This occurs when the heat index is 103 to 115 degrees Fahrenheit
Very high to extreme risk conditions = EXTREME DANGER This occurs when the heat index is greater than 115 degrees Fahrenheit.
Best Practices
Heat-related illnesses can be life-threatening, making it imperative to minimize those dangers! It is important that everyone is aware of methods to control heat stress. Anyone working in high temperatures should reduce heat stress by implementing work practice tools.
Develop and effectively communicate a work plan:
Environment assessment: Heat index, indoors/outdoors, sunlight/shade, air movement
Assess the level of physical need to perform the task at hand
Use appropriate personal protective equipment (PPE)
Plan and supervise
Buddy system: Workers care for, observe, and report each other for signs of heat intolerance
Schedule frequent breaks: Limit time in the heat or increase recovery time in a cool environment
Those not yet acclimated to working in high heat should take more breaks.
Ensure everyone knows how to recognize hazards
Reducing Risks
Provide medical aids
Prevent dehydration
Provide and drink lots of cold water
Consuming electrolytes (Pedialyte)
Eat smaller meals more often and cold meals such as salads
Adjust work schedules: Consider earlier start times, night or evening shifts, or even split shifts.
Training: All Aldridge are required to undergo Heat Stress Training before going out in the field. Workers should be able to:
Recognize signs and symptoms and be able to administer first aid
Ensure proper care and use of heat-protective clothing and equipment
Understand the effects of drugs, alcohol, preexisting health conditions
Understand the importance of immediately reporting symptoms of heat stress in oneself and others
Acclimatization
Identify who is at risk. High-risk individuals include those who have heart disease, diabetes, obesity, or use certain medication and/or alcohol.
Monitor Health
Aldridge provides job sites with cooling trailers to prevent heat stress. These are designed to move from one job site to another, containing cooling and misting fans for workers to take frequent breaks and cool down.
It’s easy to experience heat stress, but with these quick tips, you can do your best to stay prepared and vigilant in the monitoring of your health and that of those around you. Stay cool and stay safe!
Aldridge Builds Careers: Brian Mazzei
From APM to COO, Brian Mazzei has had quite a career! Brian sits down to talk about his journey to the top.
What year did you start at Aldridge and in what capacity?
I came to Aldridge in 1998 as an Assistant Project Manager (APM). At the time, we were just starting to get into telecommunications work. I remember thinking $50,000 was a lot of revenue for one division, now we consider that a small project!
From 1998 to 2009, I moved through the project manager ranks and learned how to estimate before being named Division Manager of Drilling. During this time, Aldridge acquired a caisson company on the east coast and it accelerated our expansion of foundation work across the country. By 2009, I became Vice President of our Drilling division.
Despite the recession, Aldridge continued to win major transmission line rebuild projects throughout the US. In 2014, I took over oversight of our utility division to move our internal structure to one power group. And then in 2015, the organization adjusted its corporate structure to plan for the next ten years and I became Executive Vice President.
As emerging technologies and the strain on the US power grid became more prominent, the company began to focus on additional markets within the power space that fits in with our capabilities and appetite for taking on the industry’s most challenging work. This included the expansion of our rebar capabilities as a bolt-on service, manhole assessment programs, and specialty foundation work.
After Alex Aldridge became CEO in 2021, top-level management adjusted to begin planning for Aldridge 2030. During this time, I was honored to be named Chief Operating Officer of the Power Group. Positioned for growth, Aldridge continues to make a name in the power space.
What additional skills did you work to enhance as you made your way through the ranks? Any additional schooling or certifications?
During my time as VP, I attended The University of Chicago Booth School of Business. The graduate program allowed me to hone in on my approach to leadership.
What pivotal moments help shape your career path?
I have been privileged to work alongside Aldridge legends. It was a great honor in my career to be personally mentored by Steve Rivi (CEO Emeterius) and Brian Lother (Aldridge Ambassador).
Being part of the Executive Group in 2009 really changed the way I looked at my role in the company. It taught me it was more about the health of the enterprise than just my workgroup. It was during this time that I learned that shifting culture or driving corporate initiatives took more than just a good idea, it was about total transparency to the company, clear communication, and, of course, persistence.
What corporate initiatives have you (helped) spearhead?
Throughout my 24 years with Aldridge, I have been tasked with helping to spearhead a number of corporate initiatives. I would regard these as the ones I am most proud of, for how they had a cascading effect throughout the organization.
Crew Leader Role - This newly defined role helps to identify leaders for each crew. These leaders are responsible for all on-site safety, quality, job planning, site setup, and production.
Utilizing SMEs in Safety - Identifying some of our top field performers and using their subject matter expertise in safety.
Operator Qualification Program - Using in-house SMEs as trainers, this program regularly checks the knowledge and skills of all equipment operators.
Fall Protection Policy - This safety absolute is for any drilled shaft opening that is 6 feet or more in-depth. It requires a Personal Fall Arrest System (PFAS) and a perimeter system for fall protection will be required for fall protection.
Business Manager Role - Leveraging institutional knowledge and business acumen to help drive success for each line of business
Fleet Maintenance Program - Developed regular maintenance and standardized operating procedures for the fleet of equipment.
DoForms /GoForms - In-house app that allowed for the transition from paper to electronic for important forms.
Utility and Drilling National expansion
What are your top 3 accomplishments to date?
My top accomplishments to date would have to be: the development of the Crew Leader Role, the national expansion of the Utility and Drilling divisions, and my overall growth as a safety leader. As Aldridge continues their journey to zero, I am honored to have accepted an executive position as part of the ET&D OSHA Alliance. My involvement with the alliance will help strengthen the partnership as we work to ensure safe best practices in the world of electrical transmission and distribution.
As Aldridge continues to grow, career opportunities remain plentiful. Thinking about joining the A-team? Apply now! aldridgegroup.com/careers
Navigating the River of Grass: Aldridge Electric installs transmission line foundations in the Florida Everglades
Check out Aldridge on the front cover of Line Contractor Magazine! Read about how we used our amphibious fleet of equipment to reach an otherwise inaccessible right-of-way as part of a transmission line rebuild in the Florida Everglades.
This project was a culmination of Aldridge’s appetite for risk coupled with our expertise, experience, and ability to take on the infrastructure industry’s most challenging work.
–
Headquartered in Libertyville, IL since 1952 (and in existence since 1932), Aldridge Electric, Inc. is widely recognized as one of the nation’s leading electrical contractors, especially when it comes to addressing some of the most complex and challenging projects in the transportation, power, utility, and industrial sectors. So it came as no surprise when the 1,500-employee, family-owned company was recently contracted to install new foundations for an existing transmission line for a major southeastern utility in one of the country’s harshest and most demanding environments – the Florida Everglades. Thanks to their extensive foundation experience, meticulous strategic and operational planning expertise, innovative amphibious and marine equipment, and unwavering can-do attitude, the Aldridge team completed the project safely, on time and on budget, and with a high level of quality.
As specialists in heavy infrastructure, electrical construction, foundation solutions, and emerging technologies, and more, Aldridge was tapped to work on Phase C of the utility’s “500kV Foundations Program,” which required the completion of drilled shafts for new transmission line structures in Florida that stretched along US-27 in Palm Beach & Broward County. The structures’ difficult-to-access location along the canals in the Everglades required the Aldridge team to develop alternate ways of accessing these sites using amphibious drilling equipment, barges, and boats and to find ways of navigating a broad range of hazards during the months-long project.
“Phase C was just one of 15 phases within an overall hardening program being undertaken for the utilities 500 kV system throughout the state of Florida,” shared Aldridge Division Manager Brian Schlemm.
According to Schlemm, the utility’s objective was to strengthen their system to better withstand the hurricanes and major storm events that are hitting the southern states with greater frequency and severity than ever before. “They need to bring the lines up to new standards because the storms and their winds have been getting stronger and the lines need to withstand tougher conditions than they were originally designed and installed,” he explained, Overall, “the program included the replacement of over 4,500 structures and 9,000 foundations across their service territory,” Schlemm said. “Phase C was the smallest phase of the program, but in many ways the most complex portion because of the conditions and this section of line only being accessible by water.”
A Difficult Undertaking
Kicked off in July 2021, Phase C of the 500kv Rebuild Program represented the fifth major project Aldridge had done with the utility, but by no means the easiest.
Working within a 10-mile span, “everything was only accessible via a canal that ran perpendicular to Alligator Alley, with poles sitting on little fingers off the canal,” Schlemm said. “We brought concrete, rebar cages, and other equipment out with us on boats and barges daily to pour the foundations The crews utilized four boat launches along the project to offload stage material and launch material and equipment.”
Following 3-4 months of intense planning, “the heavy equipment we used were on pontoon tracks, including a floating drill rig that allowed us to drill out the foundations while sitting on the swamp side of the structure,” shared Vice President Zach Kane of the Foundation Group. “The pontoons measured 44’ long X 7 tall X 7’ wide feet. The pontoons were installed on conventional machines that enabled us to navigate through the marsh and swamp, where water levels were 2-5’ feet high.” Kane noted that while the main canal had been dredged in the 1960s to allow the original structures to be installed off barges on the water, their current approach was decidedly more difficult due to the existing structures being in the way, lines being energized overhead, and years of sediment settling in the canals. “This time we had to work on the swamp side of the old structures, which didn’t allow the use of typical barges and conventional equipment. Low water levels also prevented the crews from being able to move larger barges down the finger canals to the structure locations,” he said. Other challenges also confronted the team of 25-30 Aldridge crew members, “One of our biggest hurdles was the heat – on average days, the temperature was over 90 degrees with 100% humidity – so safety was always a top priority,” shared Matt Rouillard, Senior Project Manager for the project. “Acclimating the crews to the heat and conditions became key for us, so we rewrote our safety protocols and limited our team’s work hours per day until they got adjusted to the weather, gradually working them up to putting in full days. We also required mandatory water breaks for hydration and installed pop-up tents to enable crew members to get out of the sun for periods of time because there are no trees or shady areas on the canals, only sawgrass, and the existing structures.”
The local wildlife presented yet another concern. “There are alligators, water moccasins, pygmy rattlesnakes, and spiders in the Everglades that we needed to watch out for – so much so that there’s an old saying in the area warning people to ‘kick it before you pick it’ to avoid getting bit,” Rouillard said.
“The weather was also an issue,” Schlemm added, “especially pop-up thunder and lightning storm cells that could impair our crews’ ability to get off the canals and safely back to the shore and cover, so monitoring those was important.”
Given the challenging nature of their environment, Rouillard confirmed that Aldridge had safety personnel and general management on site to help their teamwork through all of these issues.
Lessons Learned
Nearly seven months and 12,000 yards of concrete later, “our contract involved installing 126 structures consisting of two foundations each (for a total of 252 foundations in all), Rouillard said of the project, which the Aldridge team completed in February 2022.
While the project took more than half a year on the ground, the team credits part of its successful completion to the several months of preconstruction planning they put in beforehand.
“Our up front ordering of long lead time material like steel casing, reinforcing steel and securing equipment allowed us to avoid any supply chain delays or impacts. Kane said. “In addition, we brought in our own concrete trucks and drivers to ensure that we’d have what we needed on our schedule every day. Since we were bringing in concrete from 20 miles away and then transporting it up the canal for an hour, it was a long process and there was no time for delays.”
“This project was incredibly unique, and while there are many drilling companies out there, not all of them can go out in the water and do this type of work successfully,” Rouillard said. “We engaged in a lot of planning and trial and error to determine the best way of doing this. For example, one adaptation we made was to build and utilized a large airboat to move our rebar casing and other materials along the canal when the water levels got too low. It was all about logistics, planning, and the guys being in the right place at the right time and doing all the right things,” he said.
Schlemm reiterates that the project would not have been successful without the passionate people that make up the workforce. “Thanks to our team, everything has been readied and the foundations are set for line contractors to come in and complete the structure change outs,” Schlemm said. “We would like to thank our hardworking crews for using their innovative thinking and preconstruction planning tools to allow for a safe, well-planned project that exceeded our customer’s expectations.”
“This was a very successful project because our team stuck together and stuck to our plan,” Kane agreed. “Working together safely as a unit towards a common goal was the biggest success of the project for us and we’re thrilled with the outcome, “We currently have two other crews installing new foundations on typical transmission line right of ways in the Fort Pierce/Vero Beach area as part of Phase F of this program,” said Rouillard.
“The utility was extremely supportive and they worked closely with us to develop environmental protocols and permitting of the project to ensure that we were protecting the wetland,” Rouillard said. “In addition, we were a subcontractor for Irby Construction Company in Jackson, MS and it was a pleasure to work with their outstanding team on a project of this magnitude.”
“This project was a culmination of Aldridge’s appetite for risk coupled with our expertise, experience, and ability to take on the infrastructure industry’s most challenging work,” Kane concluded. “We leveraged the knowledge of our most seasoned employees to provide a plan, develop specialty equipment, and execute a job safely and efficiently to support our utility clients, and we pride ourselves on our innovative spirit and ability to handle what others describe as inaccessible structures.”
Former ARBTA Vice Chairman, Ken Aldridge, featured in Transportation Builder Magazine
At Aldridge, safety is a core value - a value shared from the very top. On the heels of serving as Chair to National Construction Safety Week, Aldridge Chairman of the Board, Ken Aldridge, sits down with ARTBA’s Transportation Builder Magazine.
Check out the full June issue here.
O'Brien Mills named Vice President of Safety
In a span of 21 years, O’Brien Mills has witnessed a life-altering approach/perspective on safety in both the construction industry and at Aldridge. From the Good Catch Program, to Heat Stress prevention, to our Maintenance of Traffic Program, Green Helmet & CVIS Programs, to Kask Helmets instead of Hardhats, up until our most recent Making Safe Decisions® program.
O’Brien has been a key driver behind each and every one of these initiatives and continues to look for more ways in which we can keep our employees safe. Both at home and at work, our goal has always been to be Incident & Injury Free, and it has been clear since day one that his passion reflects that lifelong commitment to Safety.
Here at Aldridge, O’Brien Mills’ 25 years of experience is crucial to the success of every project. He has been a key leader in the commitment Aldridge has to all of its employees and subcontractors. His mission is to plan, direct, and implement Aldridge’s safety and health programs to ensure a safe and healthy work environment. His official commitment to and passion for an Incident and Injury Free (IIF) workplace kicked off in early 2014 and has resulted in measurable success. Since joining Aldridge in 2001, he has been the driving force behind reducing Aldridge’s total number of Lost Work Days, even as Total Hours Worked for those same years increased by 33%. He now oversees nearly 30 employees in the safety department nationwide.
O’Brien Mills moves from his long-time position as Director of Safety, to Vice President of Safety, ready to lead and guide us into the future of an industry that may one day be completely Incident & Injury Free.
From our company to yours, Stay Safe.
Aldridge Access in the Appalachians
The following article was a featured story in
ADSC’s Foundation Drilling Magazine July/August 2022 Issue.
The US power grid is under increasing pressure as it struggles to keep up with soaring electricity demands. Work is underway across the country to upgrade the aging infrastructure to increase reliability and alleviate overall pressure on the grid. Specialty contractor, Aldridge Electric, is a utility trade partner working to help solve this problem and provide reliable power across the country.
High in the Appalachian mountains, Aldridge crews worked to upgrade existing electrical infrastructure in southern West Virginia.
The Skin Fork Area Improvement project scope of work included drilled shafts, direct embeds, and grillage foundations for a 15-mile long transmission line rebuild that spanned across three different line segments and fed into a greenfield substation. The foundation types used for this project were determined by not only soil conditions but also based on accessibility and constructability. This would prove to be the largest challenge over the course of the project for all parties involved.
Grillage foundations were used in remote locations due to the terrain not being favorable for concrete accessibility. The backfill material for those sites saw a combination of stone (which was hauled in with the use of tracked dump trucks) and native soil (that was excavated from the foundation).
The project also included the replacement of aging equipment with new technology to provide overall strength to the power grid.
Planning
At Aldridge, all projects begin with an extensive pre-job planning process that brings together subject matter experts (SMEs) from across the organization, including the estimating and project teams and field leadership.
The project timeline required a unique approach to schedule sequencing since continuous work was not possible in all of the lattice tower locations. In addition, initial mobilization was delayed nearly two years due to land acquisition challenges the utility company had to work through. Ultimately, a number of different crews had to complete the work due to the on/off schedule - sometimes with a gap of months in between.
These issues were mitigated by continued coordinated planning efforts and constant communication among the team members to recognize and handle any foreseeable problems ahead of the work schedule. Weekly meetings and pre-construction site inspections with the general contractors, environmental representatives, and construction managers allowed us to understand everyone’s expectations and work out any issues prior to commencing on-site activities.
Safety
Drilled shaft foundation work is filled with many hazards. Everyone working on an Aldridge job site has a duty to themselves and to their fellow workers to be constantly aware of potentially hazardous conditions. Each project develops a site-specific safety plan. When hazardous conditions are noted, proper action must be taken to reduce or eliminate the hazard. Safety Absolutes are implemented consistently and uniformly for all of the following job site situations: fall protection, excavation safety, confined space, energized electrical hazard, and willful or repeated violations.
One of the greatest hazards of drilled shaft foundation work is the potential to fall into a drilled shaft opening. In an effort to address this, Aldridge has developed a 100% tie-off program for fall protection. The process consists of erecting a perimeter of yellow cones and chains around the drilled shaft opening. Entry into the perimeter area is only allowed by employees utilizing a personal fall arrest system for protection. This includes a self-retracting line connected to a tie-off block. Aldridge has even designed a trapezoid tie-off block that allows for more ease while moving around a site.
For the Skin Fork Area Improvement project, there were several variances for tie-off based on the constricted site conditions. Sites were so tight that the use of standard tie-off blocks was not always available. The project team quickly identified certain pieces of earth-moving equipment that could be used instead of traditional tie-offs. This dual usage of the equipment also helped to avoid clutter on-site.
To successfully and safely complete the work on this project it took coordination from all levels and between every company involved in the build. The communication and planning as one project team was crucial. While working in remote areas, cell service and even satellite service can be unpredictable. To ensure Aldridge could communicate effectively internally and with the customer, a combination of radios, satellite phones, different cell phone providers, cell boosters, and knowledge of the area where service would be effective was utilized.
While performing nearly 40,000 work hours, Aldridge did not experience any OSHA recordable injuries.
Terrain & Location
While Aldridge is no stranger to working in remote areas, the mountainside location of this project was one of our most extreme environments to date.
It is almost impossible to describe the steepness of the terrain at each of the lattice tower locations. Coupled with the extreme weather conditions, which brought about the possibility of landslides, it seemed nearly inconceivable to develop a site-specific work plan to navigate vehicles on the narrow access roads.
Working hand-in-hand with the local utility and general contractor, Aldridge was able to navigate this challenging terrain by mitigating landslides and using off-road equipment. With the use of dozer equipment, the project team was able to deliver the necessary materials and tools to the site. This included helping drill rigs reach their intended locations and, in some areas, the use of a long reach drill rig was necessary to work around big slopes.
Logistics
Drilling in the mountains often means perforating hard rock. Specialty equipment was used to penetrate the hard rock found on many of the sites as well as for the removal of overburden. The soil and rock on the project varied vastly as the line traversed valleys, hillsides, and ridges.
Due to the site conditions at various locations, a specialized long reach drill rig was used to reach some of the direct embed foundations. This approach was used because of the way the matting pads had to be built. In addition, the use of side by sides was utilized as a tracked people mover to get into sites where rubber tire pickups could not safely traverse.
There was no single approach to hole or excavation stability that could be applied across the board. The keys to success in tackling these logistical challenges were the extensive pre-planning, constant communication, and experience of the project team with these adverse conditions. The project team was made up of SMEs and an experienced crew, all of which brought years of experience with grillages, rock excavation, groundwork, wet hole drilling, rock drilling, and mountainous terrains.
This project also added a further challenge of working around active coal mining locations which required careful logistics coordination with the utility. The use of CB radios played a huge role in the communication with the active coal trucks to ensure their drivers were aware that large earth-moving equipment would be tracking down the same access roads. Due to the current economic climate, the coal industry is booming and crews saw a record number of trucks running on the haul roads in the final months of construction.
The sheer logistics of getting the crew to the site each day was a challenge. The yard was over an hour away from the job site location - with hundreds of feet of elevation changes and a combination of paved and gravel access roads. This created cascading effects on material and concrete deliveries that were further complicated by the lack of cell phone reception. Before the hour-long drive to reach the project site, crew leaders had to use two-way radio communication to coordinate deliveries at the bottom of the mountain. Due to these extensive haul times, meticulous coordination with the crews was needed for drilling in preparation for concrete pouring.
–
In today’s connected world, it has become more important than ever to deliver safe, reliable, and resilient power across America. At Aldridge, we’re working hard every day to build and strengthen America’s infrastructure.
Changing Workplace Culture: Aldridge Mental Health & Wellness Program
May is Mental Health Awareness month and many of you might not know that the construction industry has a suicide rate that is four times greater than the national average. Construction workers are at a heightened risk for suicide for a variety of reasons that can all be addressed – starting with changing the culture in the workplace.