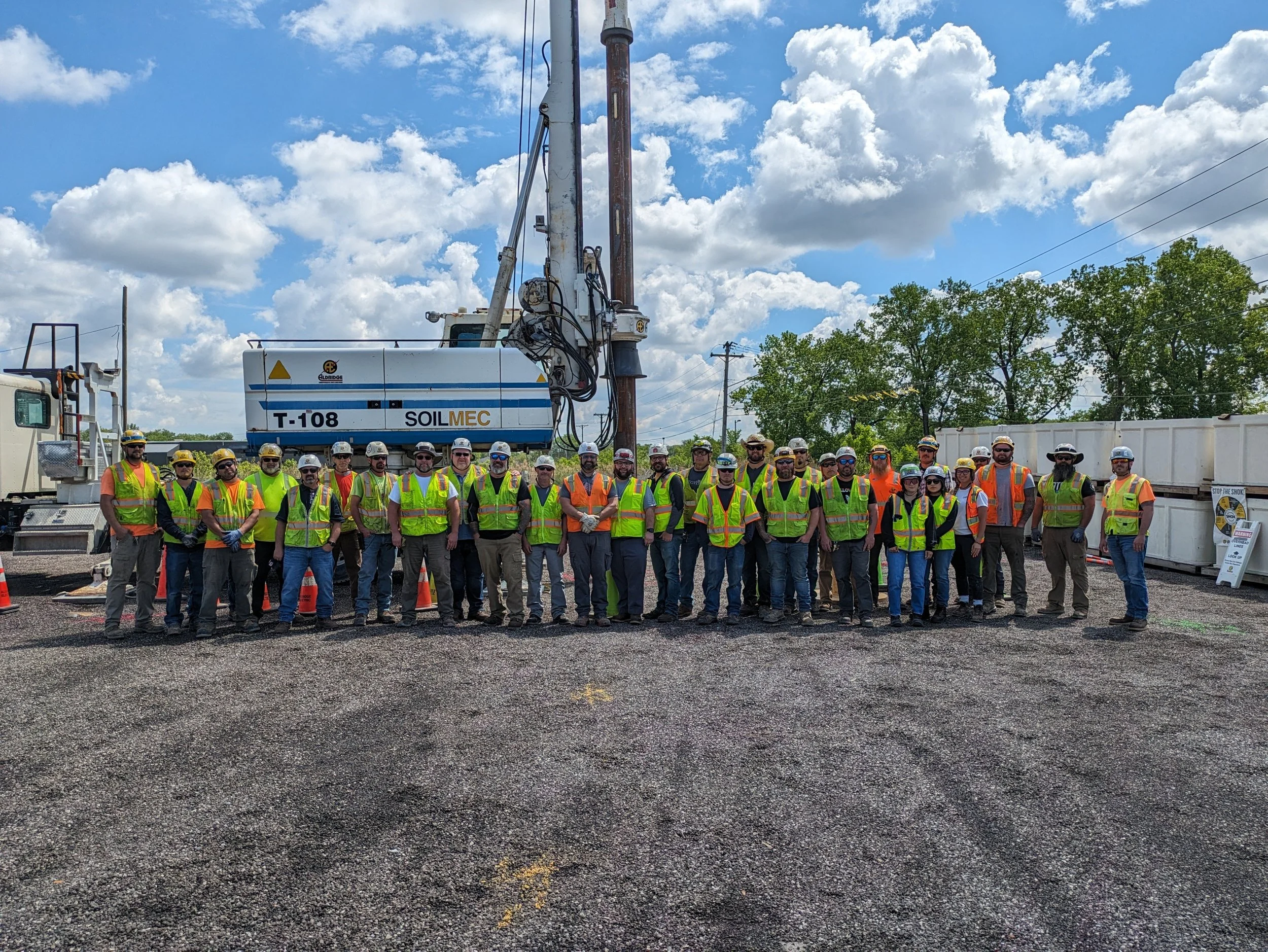
SAFETY
SAFETY CULTURE
At Aldridge, safety isn’t just a priority; it’s a core value that defines our culture. We believe in a comprehensive approach to safety that encompasses not only physical well-being but also mental health and overall wellness. While we refuse to accept injuries as an inevitable aspect of the job, we acknowledge that incidents can happen. Therefore, we’ve established layers of protection and tools to minimize their impact. Our commitment to safety transcends industry standards; it’s exemplified by our Incident and Injury Free (IIF) culture. This cornerstone propels us towards safety excellence, striving for nothing less than being recognized as a world-class organization. Our ultimate objective is clear: to foster an organization free from incidents and injuries, where every employee feels secure, supported, and valued. Our dedication to the IIF initiative doesn’t stop at the workplace; it also guides us in making safe decisions outside of work.
MAKING SAFE DECISIONS®
Culture, leadership, systems, and processes play pivotal roles in determining the level of exposure control in the workplace. However, even with robust support in these areas, human error remains a possibility due to our innate fallibility. Our Making Safe Decisions Approach enhances human performance reliability by deepening employees’ understanding of how the brain influences the recognition of SHOK exposure. It equips them with tools and techniques to mitigate brain-centered vulnerabilities, which we refer to as Brain Centered Hazards ™, including Fast Brain Functioning, Visual Recognition, Divided Attention, Memory, Social Thinking, Fatigue, and Stress and Urgency.
STOP THE SHOK
Before beginning work, our crews are trained to identify SHOK (Seriously Hurt or Killed) scenarios on their job sites. SHOK events occur due to the release or transfer of energy that cannot be absorbed safely. In the presence of high-energy exposures, it is imperative we build in the ability to fail safely. The STOP THE SHOK Program demands that we honestly assess the realities of serious injury exposures on our job sites, ensuring that successes are not left to chance and that failures do not result in fatalities. Our single and overarching objective is clear: to prevent events that jeopardize lives by averting life-threatening, life-altering, and life ending events.
The SHOK Exposure Wheel is a hazard recognition resource, identifying the eight most prevalent high energy exposures Aldridge employees encounter in their day-to-day activities. It serves as a reminder to identify and control SHOK hazards throughout all work stages; aiming to prevent exposure, and ensure a safe outcome, even in the event of failure.
SAFETY PROGRAMS
GREEN HELMET PROGRAM
The Green Helmet Program addresses the high injury risk for new employees. After orientation, new hires or those returning after a two-year absence must join the program. They receive a green helmet band and are mentored by existing employees to learn the Aldridge Way. The program includes daily training on safety practices like setting up grounds, traffic control, rigging inspection, and equipment use. Employees are evaluated at two and four weeks, and after eight weeks, they receive a final assessment. If satisfactory, they can remove their green helmet band.
SAFETY HELMETS
Aldridge is part of the first wave of construction companies to supply a new safety helmet to their employees. These helmets are at the forefront of industry standards providing an ergonomic fit for better head protection with protection against electrical shock, multiple attachable accessories, and an integrated chin strap. The strategically placed foam padding offers critical frontal, rear, and side-impact protection while the chin strap keeps the helmet in place.
By making this change, we better protect our employees and make sure that everyone goes home safe to their families every day.
SAFETY WEEK
Every year, Aldridge plays a leading role in Construction Safety Week. As a sponsor, we’re committed to recognizing our workers' dedication to safety and maintaining an injury free environment. Safety Week allows our executive team to engage with field personnel, reinforcing that safety is everyone’s responsibility.
Since 2015, we’ve held daily stand-downs and safety demonstrations at all job sites and offices nationwide during Safety Week, promoting safety awareness and sharing best practices. While Safety Week happens annually, our commitment to safety is year-round.
CRITICAL PLANNING TOOLS
Crew Leaders and Teams incorporate Critical Planning Tools into their work processes for planning and execution.
EEWP (Energized Electrical Work Permit)
DTA (Daily Task Analysis)
Critical Lift Plan
MOT (Maintenance of Traffic)
LCP (Line Clearance Permit)
Underground Damage Prevention Checklist
OSHA ET&D PARTNERSHIP
The Electrical Transmission & Distribution (ET&D) Partnership is a formal collaboration of industry stakeholders dedicated to improving safety for workers in the electric line construction industry. This unique national partnership includes government, industry, union, non-union, and trade association safety and health professionals, working together with the Occupational Safety and Health Administration (OSHA).
The Partnership’s goals and strategies include:
Performing data collection and analysis to identify causes of fatalities, injuries, and illnesses in the industry.
Developing and evaluating the effectiveness of best practices to reduce these incidents.
Ensuring the partners’ employees are effectively trained in safety and health rules and best practices.
Communicating information to enhance the safety and health culture within the electrical transmission and distribution industry.
Aldridge is proud to be a member of the ET&D Partnership, with representatives from across our organization participating in various task committees.
SAFETY INNOVATIONS
SRL Retractables
SRL Retractables
SRL Retractables
Attenuator Truck
Attenuator Truck
Attenuator Truck
Heat Stress Prevention
Heat Stress Prevention
Heat Stress Prevention